Bildquelle: Fronius International GmbH
Automatisiertes CMT-System (links), manuelles CMT-System (rechts)
CMT ist die Abkürzung für „Cold Metal Transfer“ und beschreibt einen Schweißprozess, dessen Wärmeeintrag gering ist. Der CMT-Prozess beinhaltet eine völlig neue Art der Tropfenablöse, kombiniert mit einer reversierenden Drahtelektrodenbewegung.
Beim konventionellen Kurzlichtbogenprozess wird der Draht kontinuierlich zum Werkstück gefördert. Wenn ein Kurzschluss entsteht, wird der Strom erhöht, um den Kurzschluss aufzubrechen und den Lichtbogen wieder zu zünden. Beim CMT-Prozess hingegen werden Tropfenablöse und Wiederzündung kontrolliert durch eine Rückwärtsbewegung der Drahtelektrode erzielt.
Bei diesem Beitrag handelt es sich um einen Auszug. Den vollständigen Beitrag finden Sie im Produkt „Die Schweißaufsicht im Betrieb“.
Inhaltsverzeichnis
Cold Metal Transfer (CMT): Wiederzündung mit Drahtrückwärtsbewegung
Die folgende Abbildung zeigt die Prozesszustände und den Verlauf von Drahtvorschubgeschwindigkeit, Schweißstrom und Schweißspannung des CMT-Prozesses. Der Draht wird zum Werkstück geführt, bis ein Kurzschluss entsteht und der Lichtbogen erlischt. Anschließend wird die Richtung der Drahtbewegung umgekehrt, d.h. der Draht wird vom Werkstück zurückgezogen. Dadurch bricht der Kurzschluss auf und der Lichtbogen wird wieder gezündet. In weiterer Folge wird die Drahtbewegung wieder umgekehrt und der hier angeführte Prozess beginnt von vorne.
Je nach Kennlinie für Zusatzwerkstoff, Schutzgas und Elektrodendurchmesser findet diese reversierende Bewegung in einem Frequenzbereich von 50 bis 130 Hz statt.
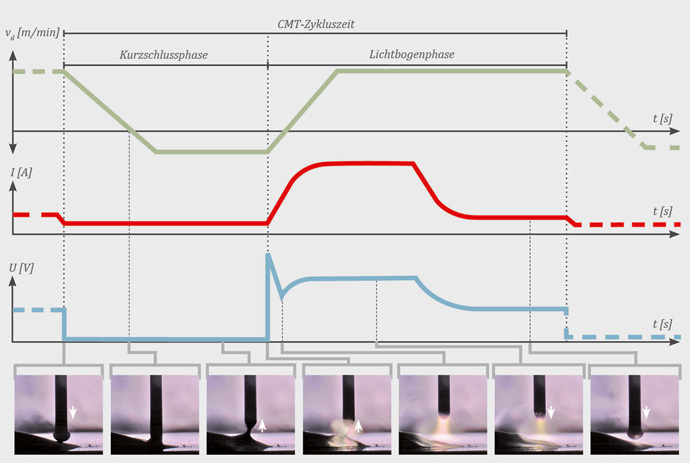
Höhere Dynamik und spezielle Stromprofilform
Seit der ersten Vorstellung des CMT-Verfahrens wurde eine Vielzahl an Kennlinien für Zusatzwerkstoff- und Schutzgaskombinationen erstellt und der Prozessalgorithmus weiterentwickelt. Die Steigerung der Dynamik der Drahtbewegung und komplexere Stromprofile erlauben eine Erweiterung des Prozessfensters in einen höheren Leistungsbereich bei gewohnt guter Prozessstabilität. Die Abschmelzrate und auch die Einbrandtiefe steigen.
Erweiterte CMT-Kennlinien
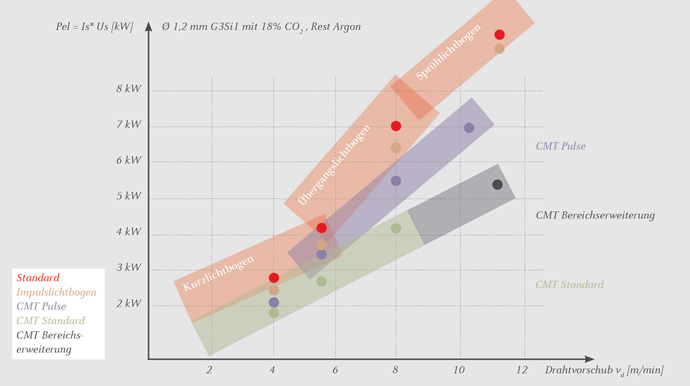
Die Abbildung zeigt die Erweiterung des Prozessfensters beispielsweise für einen Stahldraht G3Si1 (ø = 1,2 mm) mit dem Schutzgas 18 % CO2, Rest Argon. Die elektrische Leistung bei gleichem Drahtvorschub ist je nach Schweißprozess unterschiedlich. So benötigt der CMT-Schweißprozess für die gleiche Abschmelzrate weniger Streckenenergie als die Standardlichtbögen. Die neue Kennlinie der Bezeichnung CMT-Bereichserweiterung übersteigt den Drahtvorschub von 10 m/min bzw. 5 kW elektrische Leistung. Der Drahtvorschubbereich des Übergangslichtbogens wird vollkommen abgedeckt, und zwar bei einem deutlich niedrigeren Niveau der Streckenenergie.
Tiefer Einbrand mit mehr Leistung
Die Leistungssteigerung dieser weiterentwickelten CMT-Kennlinien lässt sich mit einer höheren Abschmelzleistung bei gleichzeitig größerer Tiefenwirkung für den Einbrand umsetzen. Es können nun auch dickere Bleche mit ausreichend Einbrand mit der CMT-Technologie verschweißt werden. Als Beispiel wird in der folgenden Abbildung ein Kehlnahtvergleich mit Nahtdicke a = 4 mm an 5 mm dicken Blechen gezeigt.
Grundwerkstoff: | S235; Grundblech = 5,0 mm, Stegblech = 5,0 mm |
Zusatzwerkstoff: | G3Si1; ø = 1,2 mm |
Schutzgas: | M21 = 18 % CO2, Rest Argon |
Brennerstellung: | a = 0°, ß = 45°; Stickout = 14 mm |
Nahtdicke: | a = 4 mm |
CMT Standard | CMT-Bereichserweiterung |
v2 = 50 cm/min | v2 = 75 cm/min |
vd= 7,5 m/min | vd= 11 m/min |
![]() |
![]() |
E = 4,12 kJ/cm | E = 4,08 kJ/cm |
Is = 226 A, Us = 15,2 V | Is = 271 A, Us = 18,8 V |
Der Drahtförderbereich der bisherigen CMT-Standardkennlinien für den Stahldraht (ø = 1,2 mm) endet bei vd ∼ 8 m/min. Diese Leistung zeigt am 5-mm-Blech mit der resultierenden Wärmeableitung kaum eine Einbrandwirkung. Die höhere Abschmelzleistung und Energiedichte in der Lichtbogenphase der neuen CMT-Kennlinien vergrößern die Einbrandtiefe in diesem Beispiel auf knapp 2 mm und sichern damit die Wurzelerfassung. Mit der gleichzeitigen Steigerung der Schweißgeschwindigkeit kann die Streckenenergie wieder auf ein vergleichbares Maß reduziert werden.
CMT (Cold Metal Transfer) als erfolgreiche Innovation
Der Erfolg des CMT-Prozesses spiegelt sich in zahlreichen Serieneinsätzen in einfachen, aber auch komplexen Anwendungen wider. Die Kundenanforderungen treiben letztendlich die Prozess-weiterentwicklungen voran. Neben dem vorgestellten Trend zu mehr Abschmelzleistung und größeren Blechdicken werden auch Versuche für Hybridkombinationen mit anderen Schweißprozessen unternommen.
Autor: Fronius International GmbH
Das österreichische Unternehmen Fronius beschäftigt Mitarbeiter in den Sparten Batterieladesysteme, Schweißtechnik und Solarelektronik. Bereits seit 1950 entwickelt Fronius Systemlösungen für das Lichtbogenschweißen, Widerstandspunktschweißen und die Schweißautomation.
Tipp der Redaktion
Fachbuch „Schadensfälle beim Schweißen vermeiden“
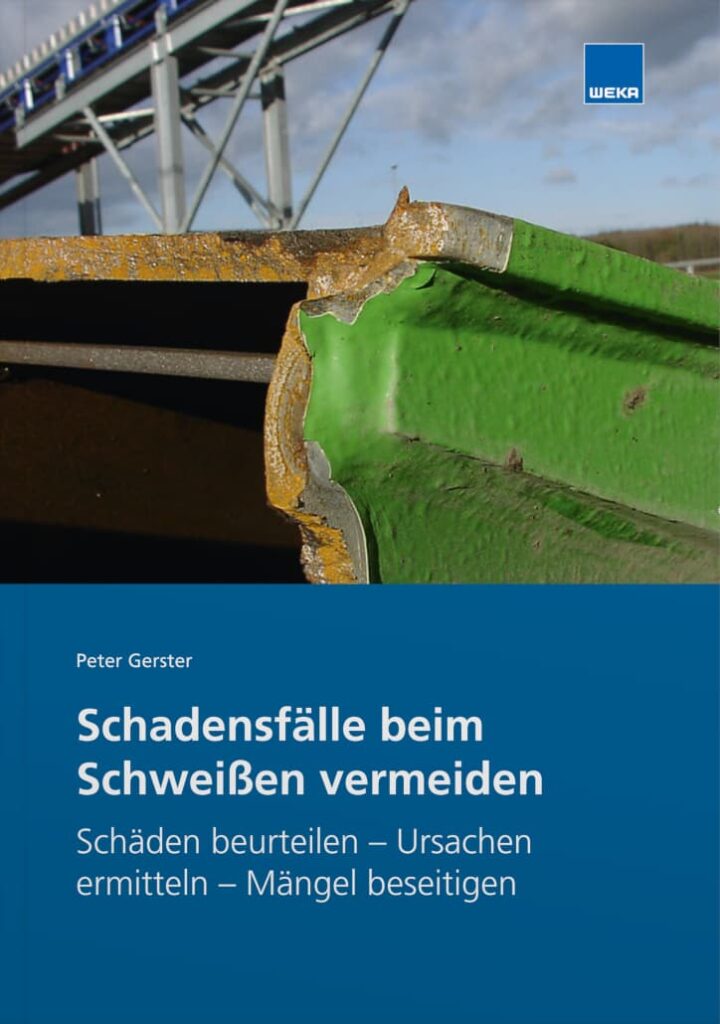
- Die Schadensanalyse
- Schadensfälle aufgrund
- von Bindefehlern und schlechter Nahtvorbereitung
- ungenügender Zeichnungsangaben
- zyklisch schwingender Beanspruchung (Ermüdungsschäden)
- der falschen Werkstoffauswahl
- wasserstoffinduzierter Kaltrisse
- Maßnahmen zur Erhöhung der Ermüdungsfestigkeit von Schweißkonstruktionen
- Maßnahmen zur Vermeidung von Schadensfällen