Bildquellen: Peter Gerster
Als Schwingbruch – auch als Schwingungsbruch oder umgangssprachlich als Dauer- oder Ermüdungsbruch – bezeichnet man den Bruch unter Lastwechselbeanspruchung. Der größte Teil aller Brüche im Maschinenbau lässt sich auf einen Schwingbruch (Ermüdungsbruch) zurückführen. Die Ermüdung des Bauteils, an dessen Ende sein Versagen bzw. der Bruch steht, ist vor allem abhängig von der Belastungsdauer und der Belastungsintensität, bedingt durch eine wechselnde Belastung. Der Schwingbruch tritt umso früher ein, je höher die Frequenz der Wechselbelastung und je größer die Schwingungsamplitude sind.
Bei diesem Beitrag handelt es sich um einen Auszug aus dem Fachbuch „Schweißnahtnachbehandlung“.
Inhaltsverzeichnis
Schwingbruch vs. Gewaltbruch
Im Unterschied zum Gewaltbruch wirken auf den Werkstoff Spannungen, bedingt durch schwellende oder schwingende Belastung, ein, die unterhalb der Streckgrenze, also im elastischen Bereich, liegen. Unter solchen Wechselbeanspruchungen lassen sich z.B. bei einer ausreichenden Zahl von Lastwechseln mikroplastische Vorgänge und Veränderungen in der Mikrostruktur des Werkstoffs feststellen, die ein Indiz für die Ermüdung sind.
Rastlinien
Rastlinien sind das sichtbare Kennzeichen für einen Schwingbruch (Ermüdungsbruch) und sie lassen das zyklische Risswachstum auf der Bruchfläche erkennen. Das mikroskopische Gegenstück dazu sind sehr fein strukturierte Furchen, die als Schwingstreifen bezeichnet werden.
Tipp der Redaktion: Lesen Sie auch den Schadensfall „Sanierung einer Staukappe“
Nachfolgend wird ein Beispiel für einen typischen Schwingbruch (Ermüdungbruch) aufgeführt.
Beispiel: Schwingbruch an einem Baggerausleger
An einem Bagger, der im Umschlagbetrieb eingesetzt wurde, entstand nach relativ kurzer Zeit ein Bruch des Auslegers.
Zur besseren Krafteinleitung wurde der Ausleger im hoch beanspruchten Bereich mit Versteifungsblechen verstärkt. Die folgende Abbildung zeigt den Dauerbruch auf der gegenüberliegenden Bruchseite. Sehr schön sind die entstandenen Rastlinien des Dauerbruchs zu erkennen.
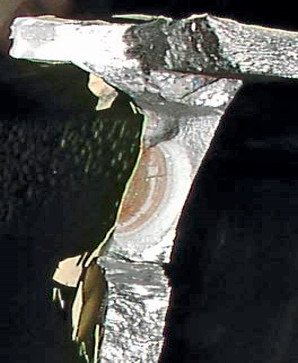
Hohe Zugeigenspannungen durch den Schweißprozess
Wie in der folgenden Abbildung sehr gut zu sehen ist, beginnt der Dauerbruch genau am Ende des Versteifungsblechs an der Querschweißnaht. Der Bruch beginnt exakt an dem Schweißnahtübergang zum Grundblech.
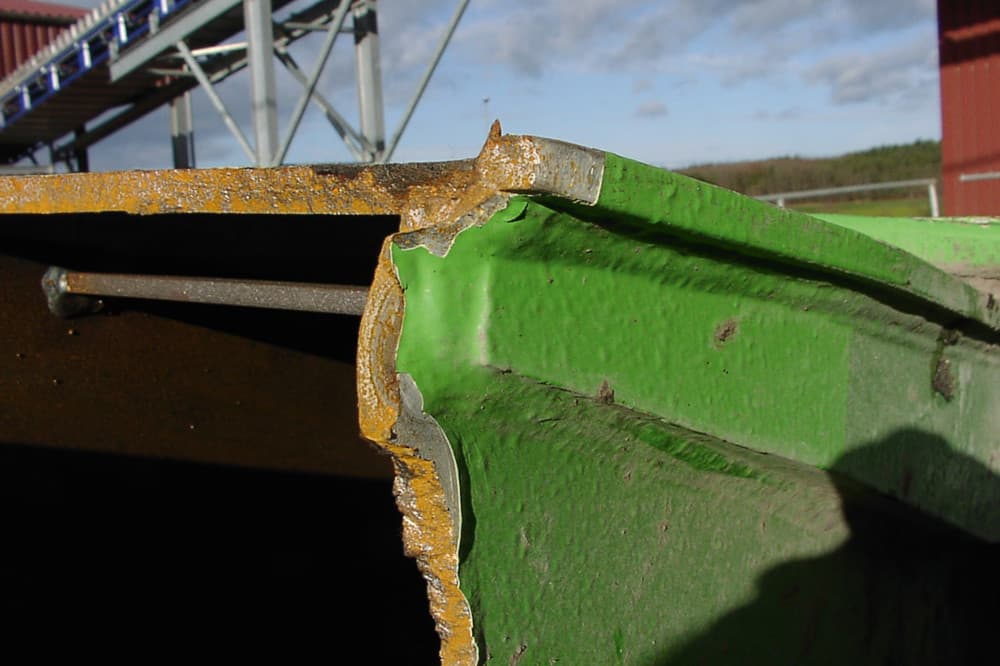
Die Ursachen liegen einerseits in den sehr hohen Zugeigenspannungen im Nahtübergang und andererseits in der Kerbwirkung der Schweißnaht.
Die hohen Zugeigenspannungen entstehen durch die Schrumpfwirkung (Schrumpfungsbehinderung) beim Schweißen. Durch wissenschaftliche Messungen der Zugeigenspannungen weiß man sehr genau, dass diese bis zur Höhe der Streckgrenze reichen können. Bei dünnen Blechen äußern diese sich durch
den Verzug, der bei dicken Blechen nicht stattfindet.
Lösung: Schweißnahtnachbehandlung
Die Kerbwirkung wird durch die Form der Bauteile sowie die Nahtform beeinflusst. Außerdem können durch den Schweißer zusätzliche Einbrandkerben entstehen. Durch geeignete Schweißnahtnachbehandlungen lassen sich sowohl die Zugeigenspannungen als auch die Kerbwirkung verbessern.
Durch Verstärkungs- und Versteifungsbleche entstehen bei ungünstiger Gestaltung sogenannte Steifigkeitssprünge, an denen sehr hohe Spannungsspitzen entstehen. Zusammen mit den hohen Zugeigenspannungen wird die zulässige Spannung sehr schnell überschritten und der Ermüdungsriss kann beginnen. Dies wird umso gravierender, je näher die Quernähte in die höchste Zugzone kommen.
In diesem Schadensfall wäre es besser gewesen, die Längsschweißnaht in das Stegblech auslaufen zu lassen und keine Quernaht zu schweißen.
Fazit zu den Schadensursachen
- Es findet sich ein großer Steifigkeitssprung am Ende des Verstärkungsblechs.
- Die Quernaht befindet sich in der höchstbeanspruchten Zugzone.
- Es wurde keine Schweißnaht-Nachbehandlung durchgeführt.
Autor: Peter Gerster