Roboterzellen zum MSG- und WIG-Schweißen sind meist in Großbetrieben für Bauteile in hohen Losgrößen zu finden. Um eine möglichst hohe Produktivität zu erreichen, sind diese Anlagen auf kurze Taktzeiten und eine hohe Präzision optimiert. Die vom Roboterhersteller speziell für das Schweißen verfügbare Software erleichtert die Integration der Schweißstromquelle, die Inbetriebnahme der Anlage und das Einrichten neuer Bauteile. Zusätzlich bietet die Software oft noch spezielle Funktionen für das Schweißen, wie z.B. verschiedene Arten der Pendelbewegungen oder eine Regelung zur Nahtverfolgung. Dies erhöht allerdings die Komplexität und den Aufwand für das Einrichten neuer Bauteile. Dadurch werden hier Spezialisten benötigt, die im Umgang mit dem Roboter geschult sind und gleichzeitig Erfahrung in der Schweißtechnik haben.
Vorteile beim Einsatz eines Cobots
Für kleine und mittelständische Unternehmen mit geringeren Losgrößen und häufigem Bauteilwechsel stellt eine solche klassische Roboterzelle meist keine optimale Lösung dar. Denn im Verhältnis zur kürzeren Schweißzeit ist die Umrüstzeit bei neuen Bauteilen relativ groß. Zusätzlich spielen auch die Investitionen in die Anlage selbst, als auch in Schulungen der Mitarbeiter, eine nicht zu unterschätzende Rolle. Als Folge werden auch einfache Bauteile in relativ großen Stückzahlen durchaus noch manuell geschweißt.
Durch Einsatz eines Cobots können folgende Vorteile erschlossen werden:
- intuitive Bedienkonzepte der Cobots erleichtern das Einlernen des Bedieners
- Handführung an die gewünschte Position erleichtert die Programmierung der Schweißaufgabe
- damit können neue Bauteile relativ schnell eingelernt werden
- kurze Einstellzeiten erlauben wirtschaftlichen Bauteilwechsel
- Entlastung der Schweißer von monotonen und anstrengenden Arbeiten
Kleine bis mittlere Serien, welche bisher in wenigen Tagen bis Wochen manuell gefertigt wurden, können mit dem Cobot kostengünstiger gefertigt werden. Der entlastete Schweißer kann sich zudem mehr um anspruchsvollere Einzelstücke und Kleinstserien kümmern.
Entwicklung kollaborierender Roboter (Cobot)
Seit Jahrzehnten werden Industrieroboter permanent weiterentwickelt. Eine der neueren Entwicklungen sind Leichtbauroboter für die Mensch-Roboter-Zusammenarbeit. Dank moderner Sicherheitstechnik können „Kollaborierende Roboter“ (lat.: co- ‚mit-‘, laborare ‚arbeiten) in direkter Interaktion mit dem Menschen arbeiten. Großräumige Schutzeinrichtungen sind nicht mehr notwendig, sodass ein solcher Roboter relativ schnell und einfach eingebunden werden kann. Dadurch ist er auch für viele Schweißfachbetriebe attraktiv, deren bisherige Arbeitsabläufe überwiegend für das manuelle Schweißen ausgelegt sind.
Seit der Mitte des 20. Jahrhunderts sind Industrieroboter im Einsatz. Zum Schutz des Arbeiters werden diese seitdem in Schutzzellen eingehaust. Seit einigen Jahren steht ein besonderer Typ, der kollaborierende Roboter oder kurz Cobot zur Verfügung. Damit sind Anwendungen möglich, in denen Mensch und Roboter gleichzeitig im selben Arbeitsraum zusammenarbeiten. Dies wird durch moderne Sicherheitstechnik und häufig auch durch eine besonders leichte Konstruktionsweise des Roboters erreicht. Daher steht oft auch der Begriff Leichtbauroboter (LBR) im Zusammenhang zur Mensch-Roboter-Kollaboration (MRK)
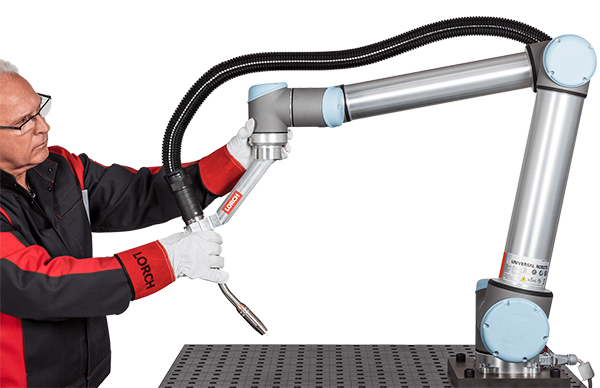
Die Stärken eines kollaborativen Roboters
Bei Cobots steht die Sicherheit des interagierenden Mitarbeiters an erster Stelle. Der wichtigste Aspekt dabei ist, dass Menschen nicht durch auf sie einwirkende kinetische Energie verletzt werden. Da kinetische Energie von zwei Faktoren abhängt, der Bewegungsgeschwindigkeit und der Masse des bewegten Gegenstandes, sind Cobots heute typischerweise Leichtbauroboter.
Im Vergleich zu den Industrierobotern, die herkömmlicherweise im Bereich Schweißen eingesetzt werden, bringen sie nur 15 – 20 % des Gewichts auf die Waage. Eventuell damit einhergehende Einschränkungen bei den Traglasten sind für den Bereich Schweißen nicht relevant. Bedeutsamer ist für das Schweißen der Umstand, dass die Cobots hinsichtlich Wiederholgenauigkeit von Bewegungsabläufen und -sequenzen keine gravierenden Abstriche machen und somit eine vergleichbare, reproduzierbare Qualität gewährleisten wie ihre großen Brüder.
Heutzutage sorgen bei Cobots integrierte Sicherheitstechnik und leistungsfähige Sensorik dafür, dass sie schon bei leichtem Kontakt umgehend ihre eigene Bewegung stoppen und somit Schäden bzw. Verletzungen vermieden werden. Insgesamt wird dies unter dem Thema Leistungs- und Kraftbegrenzung durch inhärente Steuerung zusammengefasst. Es gibt dabei auch Ansätze, herkömmliche Industrieroboter für kollaborative Tätigkeiten zu ertüchtigen, z.B. durch zusätzliche weiche Sensorik-Außenhäute. Für den Bereich Schweißen sind diese Alternativen aufgrund der spezifischen Belastung durch UV-Strahlung bzw. Funkenflug und Schweißspritzer aus heutiger Sicht jedoch nicht geeignet.
Herkömmliche Industrieroboter punkten dadurch, dass sie in einer Schutzumgebung eingehaust sind und auf maximale Bewegungsgeschwindigkeit getrimmt werden können, also immer dort vorteilhaft sind, wo die Optimierung der Taktzeit im Vordergrund steht. Aus diesem Grund bleiben die herkömmlichen Industrieroboter weiterhin das Maß der Dinge, wenn es um sich häufig wiederholende, vollautomatisierte Großserien mit relativ geringer Bauteilvarianz geht.
Allerdings weisen dieselben Roboter Defizite auf, was die Fertigung von kleineren und mittleren Losgrößen und einzelauftragsspezifischen Bauteilen angeht. Hier ist weniger die Taktzeit als vielmehr die Optimierung der Einstellzeit der kritische Erfolgs- bzw. Kostenfaktor für eine effizient automatisierte Fertigung. Beim Schweißen gilt dies in verstärktem Maße, da die beim Schweißen typischen Verfahrgeschwindigkeiten generell eher niedrig und für herkömmliche Roboter sowie Cobots gleich sind.
Vor allem bei der Reduzierung der Einstellzeit bieten die Cobots entscheidende Vorteile: einerseits durch ihre modernen, einfachen und intuitiven Bedienkonzepte als auch durch die Möglichkeit die Cobots per Handführung in die gewünschten Positionen zu bringen.
Autoren: H. Tran und P. Spronken
Den kompletten Fachbeitrag finden Sie in „Die Schweißaufsicht im Betrieb“
Bildquellen:
- A. Rimböck und P. Spronken, „Praxis-Ratgeber Cobot-Schweissen“, Lorch Schweißtechnik GmbH, Auenwald, 2019
- Kollaborativer Roboter (Cobot) zum Schweißen in Leichtbauweise: H. Tran und P. Spronken, „Kollege Roboter – Hand in Hand mit dem Schweißer“, Vortrag auf DVS Congress 2019